However, to get the best results from your knitting machines, it is essential to understand how to increase production without compromising the quality of the fabric.
Circular knitting machines can make weft-knitted fabric structures (warp knit), they are a popular choice for producing knitted fabrics, especially in the apparel industry.
In this article, we will discuss several strategies to improve productivity with your circular knitting machine in the knitting industry, including the following:
I. Invest in Automatic Machine Lubrication System:
To keep your circular knitting machines running smoothly and efficiently, install automatic machine lubrication systems that can ensure smooth operation and reduce maintenance downtime.
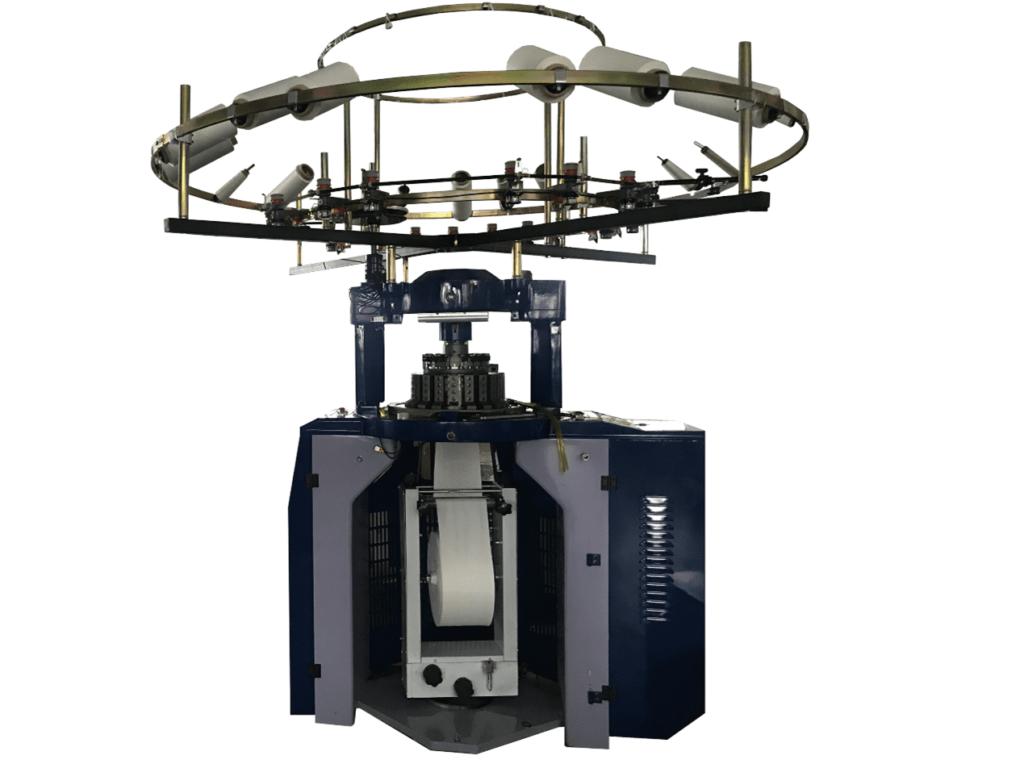
Circular knitting machines require regular lubrication to ensure smooth operation and reduce wear and tear on the machine’s moving parts.
Lubrication helps to prevent friction and overheating, which can result in downtime, increased maintenance costs, and even machine failure.
Therefore, investing in an automatic machine lubrication system can bring several benefits to get higher production, such as:
1. Reduced Downtime: An automatic machine lubrication system ensures that the machine’s lubrication needs are met even while the machine is running, which reduces downtime associated with manual lubrication.
2. Consistent Lubrication: Automatic machine lubrication systems apply a precise amount of lubricant to each lubrication point on the machine, ensuring that every part is adequately lubricated. This consistency of lubrication eliminates the risk of under or over-lubrication which can harm machine efficiency and harm the knitting process.
3. Better Quality Output: Improper lubrication can result in poor-quality output due to the impact on the machine’s efficiency and wear, which can lead to the poor fabric quality. The lubrication system ensures that the machine is running smoothly and efficiently, leading to better fabric quality output.
4. Extended Knitting Machine Life: lubricating the machine adequately ensures the machinery’s longevity, reducing the need for component replacement and spare parts, and helping maintain the value of the initial investment.
5. Reduced Maintenance Costs: Proper knitting machine lubrication helps to minimize wear and tear on your knitting machine’s moving parts, reducing the frequency of maintenance tasks associated with mechanical failure.
II. Improve Yarn Feed Control Device:
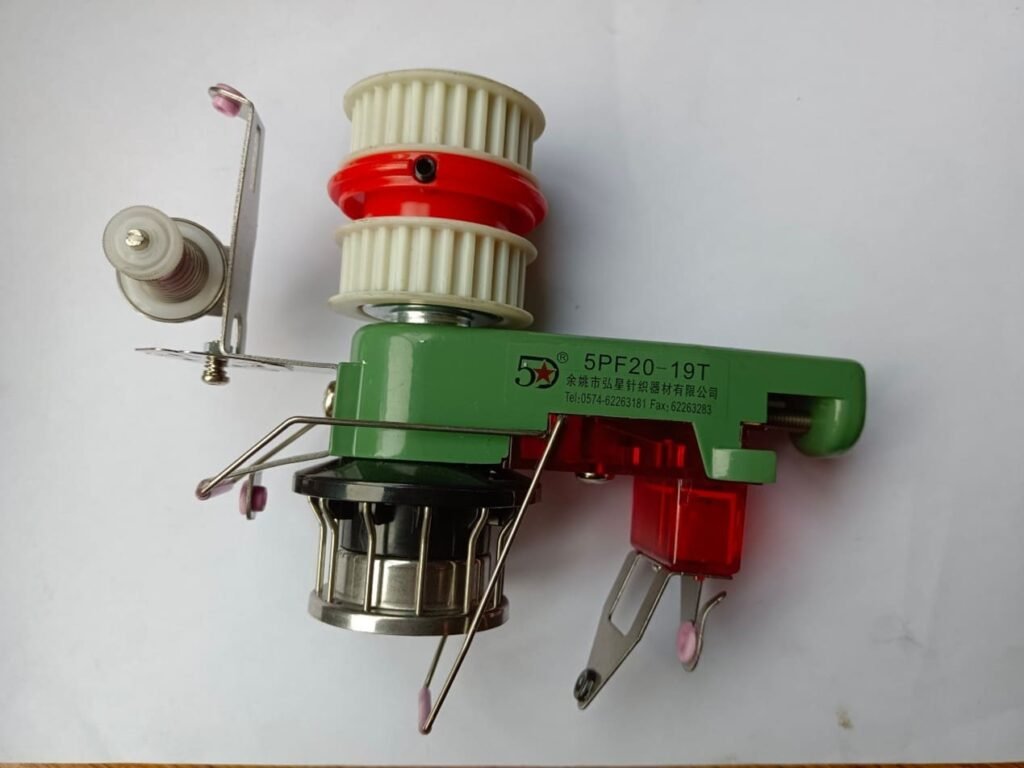
The yarn feed control device plays a very significant role in the knitting process, and by ensuring it works correctly and applying yarn supply with a creel feeding system instead of the plastic tube, you will improve productivity while maintaining quality.
The yarn feed control device plays a crucial role in the knitting process by ensuring that the yarn is fed uniformly and at the correct rate to the knitting needles. Any issues with the yarn feeding system can result in yarn tangling, broken yarns, or fabric defects, which can cause production delays and reduce the quality of the final fabric product. Therefore, improving the yarn feed control device is essential to increase the production rate while maintaining the consistency and quality of the fabric.
One of the ways to enhance yarn feed control is by using a creel feeding system instead of a plastic tube. A creel feeding system offers better control over the yarn’s tension and minimizes the possibility of the yarn tangling, broken yarns, or fabric defects by consistently providing the same feed regardless of the transfer angle.
Another essential part of yarn feed control is ensuring that you’re using suitable yarns that work with the circular knitting machine’s specifications. The type of yarn used, the yarn count, and the machine gauge can all affect the machine’s production speed and quality. Therefore, using the appropriate type of yarn and controlling the yarn’s tension will optimize the yarn feed control.
It is also vital to keep the yarn feed control device well-maintained by regularly cleaning and lubricating it. Proper maintenance will minimize potential faults the device might create that could negatively affect the knitting process.
In conclusion, improving the yarn feed control device on your circular knitting machine has a significant impact on the production rate and fabric quality. By using a creel feeding system, maintaining consistent tension, using the appropriate type of yarns that work with the circular knitting machine’s specifications, and ensuring proper maintenance on the yarn feed control device, you can enhance production speed, and efficiency and maintain the fabric quality.
III. Optimize Circular Knitting Machine Gauge:
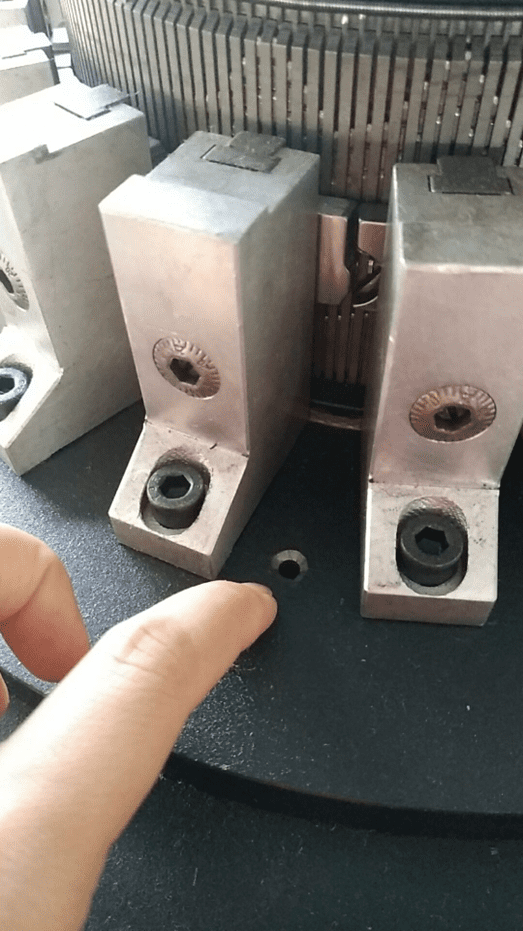
The knitting machine gauge, or the number of needles per inch, can affect the knitting speed and fabric quality. Using a higher gauge machine can help you achieve higher production rates and can also result in the better quality fabric due to higher air permeability.
The knitting machine gauge refers to the number of needles per inch on a circular knitting machine. The gauge directly affects the production rate and fabric quality of the machine. Optimization of the knitting machine gauge can be done to increase the production rate and maintain quality.
Using a higher gauge machine can increase the machine’s production speed due to the decrease in stitch width, resulting in more stitches per inch, leading to a higher fabric production rate. However, operating a higher gauge machine requires precise yarn tension control that such machines need to prevent yarn tangle, needle breakage, or needle bend, which can delay production.
Consequently, as the gauge increases, the machine’s air permeability also increases, making it more likely to create fabrics with better air permeability. However, a quality reduction is bound to happen if the machine’s gauge is too high, arguably leading to issues such as weight or mass, color inconsistency, or laddering.
Moreover, the machine gauge should match the type of fabric to be produced. Machine gauges are typically categorized as standard, fine, ultra-fine, or super-fine. Standard gauge machines are useful for producing heavier fabrics like denim, while fine and ultra-fine gauges can handle finer fabrics, like lightweight and delicate knit fabrics.
Designers and machine operators, therefore, need to always consider the fabric’s end use and, more importantly, the raw material fiber length, thickness, and structure before they choose a machine gauge. The type of raw material will affect the machine stitch and fabric quality when choosing the right stitch setting/parameters.
In conclusion, the optimization of the circular knitting machine gauge is crucial in improving the production rate and fabric quality. The machine gauge can increase the machine’s air permeability, enabling it to produce fabrics with better air permeability. However, designers and machine operators must always consider the fabric’s end use, raw material fiber length, thickness, and structure before choosing a machine gauge. If done right, optimizing the machine gauge can lead to a better return on investment in the long run.
IV. Control Yarn Tension:
Excess tension can lead to yarn damage, production loss, and poor fabric quality. Therefore, controlling the yarn’s tension to prevent it from imposing excess tension is crucial.
Yarn tension refers to the amount of force applied to the yarn during the knitting process. Properly controlling yarn tension is crucial to producing high-quality fabrics with fewer defects and avoiding production problems such as broken yarns, tangles, or uneven fabric.
One of the most common ways to control yarn tension on a circular knitting machine is by using a tension regulator. The regulator can be used to adjust the tension manually, made electronically, or automatically maintained at the optimum tension for each yarn. The regulator can be adjusted to compensate for changes in the yarn’s elasticity or stiffness, and it can be calibrated to account for different yarn types and stitch structures. The target tension force should be achieved uniformly throughout the yarn feed process.
It is also important to ensure that the yarn tension is not too high. Excess yarn tension can cause damage to the yarn or fabric, resulting in quality issues such as fabric pilling or breakage, which wastes materials and cause production delays. Over-tensioned yarn on the other hand can impact the machine’s performance leading to longer machine downtimes when replacing broken needles or clearing knitting ladders.
To avoid over-tensioned yarn, it is best to work with small batches of yarn during the testing phase and use a tension monitor to check the tension regularly. By checking and adjusting the yarn tension regularly with precision, you can produce fabrics with fewer defects, reduce wastage and minimize production downtime from machine errors.
In conclusion, proper yarn tension control is essential for producing high-quality fabrics and avoiding production problems. By using a tension regulator, checking yarn tension regularly, using small batches and cooperating with the yarn specifications, and setting the value of the gauge right, adjusting the stroke order settings and cam arrangement settings accordingly, the smallest adjustment can maximize the production quality improvement. Remember that the quality of the fabric is based on the basics of the circular knitting machine’s optimization for each fabric type, ensuring the fabrics’ best quality, and uniformity, and maintaining production efficiency.
V. Implement Effective Cam Arrangement Settings:

By experimenting with different cam arrangement settings and understanding textile design production, you can determine the best setting to achieve your target production rate.
Cam arrangements are critical elements of circular knitting machines that guide the needle and sinker movements during the knitting process. Adjusting the cam arrangements can significantly affect the machine’s production rate, the quality of the fabric output, and the machine’s operating life span. As a result, it is crucial to implement effective cam arrangement settings for your machine.
Many different cam arrangement settings can be adjusted, such as loop length, stitch density, stitch width, and stitch angles. The settings you choose will depend on the fabric you intend to produce, and it is essential to understand the impact of each adjustment on production efficiency and fabric quality. For example, setting the loop length can improve fabric softness, while adjusting the stitch density can improve fabric weight.
During the knitting process, adjusting the stroke and cam arrangement settings can increase the production rate output of your circular knitting machine while maintaining consistent quality. That said, precisely setting the cam arrangement settings may require technical expertise, and the operators/specialists/designers need to stay current with machine and software updates.
It is also essential to regularly calibrate and maintain the cam arrangement settings to ensure they remain effective over the long term. It’s best to have regular checkups, test different settings, analyze production data regularly, and develop contingency plans to troubleshoot any possible errors or downtime issues.
In conclusion, implementing effective cam arrangement settings can significantly improve the production efficiency and fabric quality of your circular knitting machine. By considering various factors such as stitch length, stitch density, stitch width, and stitch angles when adjusting cam arrangements, you can achieve different objectives with the fabric produced. Also, calibrating and regularly maintaining the settings is key in ensuring that the settings remain effective over the machine’s lifetime. Be sure to keep up-to-date with any changes in management strategy or technological advancements in the industry to build a well-informed team of machine operators who are aware of what settings work best for each particular knitting floor.
VI. Maintain the Knitting Floor Environment:
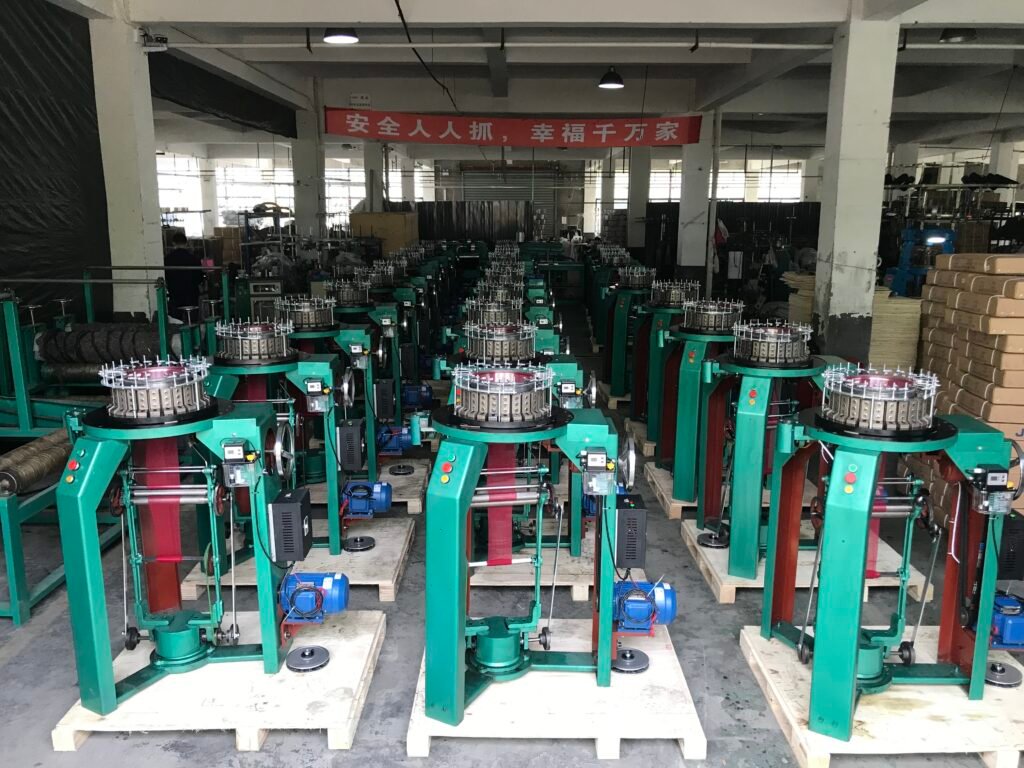
The knitting floor environment plays a crucial role in the production process. Keep the knitting floor clean, away from noises & vibrations, and ensure proper ventilation to control dust particles, maintain a steady temperature & humidity level, and thus minimizing yarn damage, rising air resistance, and knitting machine downtime.
1. Temperature and Humidity: Circular knitting machines are sensitive to temperature and humidity changes. It is important to keep the knitting floor at a consistent temperature and humidity level to prevent damage to the machine and ensure smooth operation. Consider investing in air conditioners or dehumidifiers to maintain the ideal environment.
2. Lighting: Proper lighting is important for working with delicate yarns and fabrics. Ensure that the knitting floor has adequate lighting to prevent eye strain and enable operators to see their work.
3. Organizing Supplies: Organizing and labeling yarns, fabrics, and other supplies can make it easier for knitting machine operators to find what they need quickly, saving time and reducing frustration.
4. Regular Cleaning: Regularly removing dust and debris from the knitting floor can help to maintain a clean and safe environment. Dust buildup can also cause problems with the knitting machine, so cleaning should be a part of routine maintenance.
5. Preventative Maintenance: In addition to regular cleaning, it’s important to take proactive steps to prevent issues before they occur. This includes regular inspections of the knitting machines and identifying and addressing any potential problems before they escalate.
By maintaining a clean, organized, and consistent environment on the knitting floor, operators can focus on knitting and get more done in less time, leading to increased productivity.
VII. Train Circular Knitting Machines Operators:
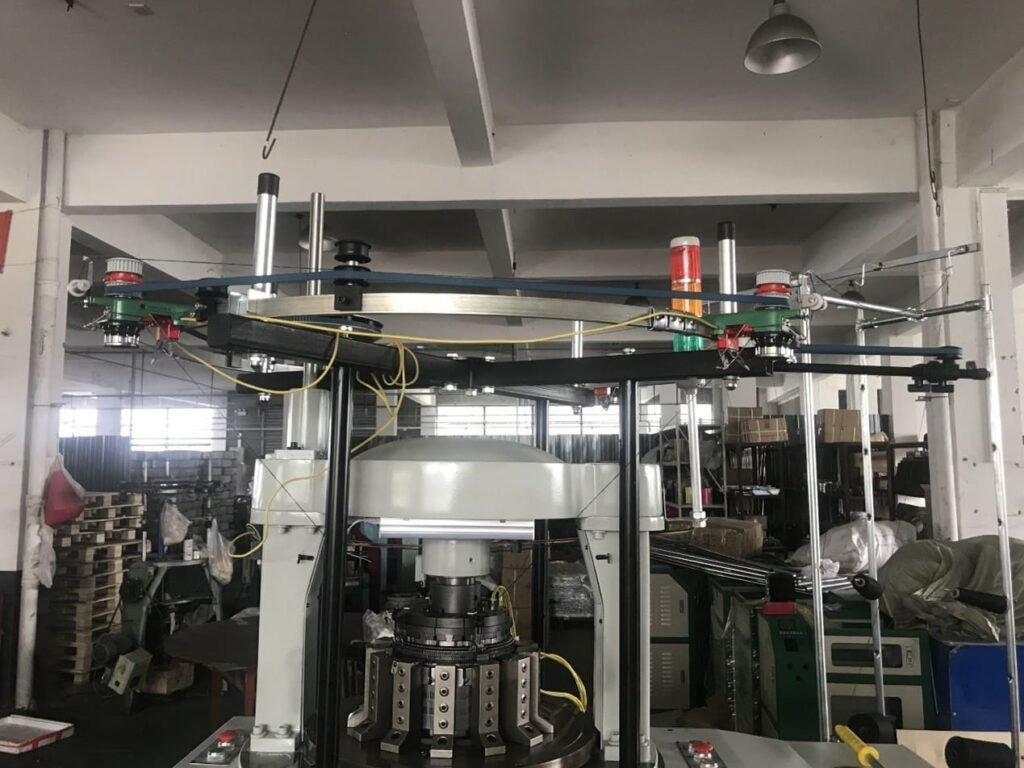
Circular knitting machine operators play a significant role in production management. Properly training knitting machine operators on machine usage, Fabric Quality Control (FQC), machine maintenance, and ensuring different cam arrangement settings are set correctly can improve productivity.
Machine operators play a crucial role in maximizing the productivity of circular knitting machines. By properly training your machine operators, you can ensure that your machines are running efficiently, reducing downtime, and fabric defects, and optimizing production rates.
Effective training should cover basic machine operation, different machine models (e.g double jersey knitting machines, circular knitting machines), and maintenance, with an emphasis on safety, troubleshooting, and reporting machine faults. Ensure that your machine operators are trained to conduct visual inspections, troubleshoot common defects like yarn breakages, and be able to resume production while minimizing quality loss.
Machine operators should also understand how to optimize machine settings, adjust machine parameters, implement machine operation data analysis, and properly allocate skilled labor on your shop floor. It is essential to train your operators to understand that the machine settings and stitch configuration settings are unique for specific yarn specifications and fabric types.
VIII. Monitor Production Data and Set Production Targets:

By monitoring production data, you can identify areas where you could improve productivity while maintaining quality. Set realistic production targets and implement steps to achieve them. Here are some additional points:
1. Data Collection: Collecting data on production rates, machine downtime, and other factors can help identify opportunities for improvement. Tracking data over time can also help to identify patterns or trends that may be impacting productivity.
2. Establishing Targets: Setting production targets based on historical data or industry benchmarks can help to focus efforts on areas that need improvement. It can also provide a clear goal for operators to work towards, which can motivate them to strive for higher productivity levels.
3. Regular Reviews: Regularly reviewing production data and targets can help identify areas where progress is being made and where more work is needed. It can also provide an opportunity to make adjustments to the production process or set new targets to keep pushing productivity forward.
4. Identifying Bottlenecks: Production data can also be used to identify bottlenecks in the production process. This can help operators to identify areas where improvements can be made to increase productivity, such as adjusting machine settings, optimizing the flow of materials, or reorganizing the workspace.
5. Incentives: Setting up incentives or rewards for achieving production targets can also motivate to increase productivity levels. This can include bonuses, recognition, or other incentives.
By monitoring production data and setting production targets, operators can focus their efforts on areas that provide the best opportunity for improving productivity. This can lead to more efficient use of time, materials, and machinery, ultimately leading to increased production output.
By following the above-mentioned steps, increasing your circular knitting machine’s productivity, and ensuring better quality and fast production can be done efficiently. Research recommends that there are other developments such as dip das designed to improve knit fabrics, but the factors listed above are some basics that create a fundamental part of designing knit fabrics.
In conclusion, with the right strategy, understanding of the machine gauge, adopting an effective driving system, knitting machine accessories and knitting machine maintenance, and knitting floor management, it is possible to increase production on circular knitting machines while maintaining good fabric quality. Be mindful of other factors, such as the yarn count, flat bed knitting machine, double jersey knitting machine, and single jersey, but by optimizing machine settings, implementing improvements, and regular product development, you can meet your production goals and achieve better outcomes for your business in the textile knitting industry.